Mechanical agitator granulators as the name implies are granulators that by virtue of agitator speed, sweep volume, or bed pressures, generate relatively lower shear which has implications on the operating conditions and resultant granule properties. Mechanical agitator granulators can also be referred to as low shear granulators.
During granulation process, the active compound and other excipients are combined with a binder solution to form granules with a fixed composition through rotating low-shear forces via low-power-per-unit-mass with addition of a liquid.
For reasons of space, only a short conveyor belt and a hopper with lower inlet-height could be applied for the granulator II. The longest parts will therefore be granulated on granulator I. Granulator I: Throughput 1400 lb/h, size of granulate 5 ± 1mm Parts with dimensions of up to 72' x 32', diagonal 80' Part weight up to 12 pounds. Roller Press Granulator is the key equipment of compound fertilizer granulation, its working principle is: the motor drive the belt and pulley, transfer to the drive shaft through the speed reducer, through the open gear synchronously with the driven shaft, the double rollers rotate in the opposite direction. Pan granulator machine can make different fertilizers with various materials. With different raw materials, you can make both organic fertilizer and compound fertiliser. You can produce organic fertilizer with materials such as, chicken poo, cow dung, sheep manure and so on. If you have much animal wastes but you don’t know how to handle them.
Mechanical agitator granulators are generally characterized by; Rocketdock skin packs.
- Longer run time
- Lower density and higher porosity granule yield than those of high-shear granules.
- Their tendency of compressing the granules and reduced void volume as a result of their design.
- Their requirement of additional binder solution for granulation processes.
Contents
Subclasses of mechanical agitator granulators
The subclasses of wet low-shear granulator/ mechanical agitator granulators are primarily distinguished from one another by the geometry and design of the shear inducing components. Granulators which operate by mechanical agitation include the following;
- Ribbon or paddle blender.
- Planetary mixer.
- Orbiting screw mixers
- Sigma blade mixer
Shear is induced by either rotating impeller, reciprocal kneading action, or convection screw action.
i. Ribbon or Paddle Blender
Ribbon blender popularly used as a dry mixer can serve as a very reliable granulator if a dry paste is formulated for the machine. The following is worthy of note when using a ribbon or paddle blender as a granulator;
- Most ribbon blenders are not designed to withstand the shift torque required for granule formation and for this reason one should make sure that the granulator shaft is strong enough before carrying out a granulation process in a ribbon blender designed for dry mix.
- When the kneading time is extended (above normal), the granules are densified and this leads to increased moisture exposure, increased particle size, and reduced porosity.
- The tendency of the material to adhere to the side well is pronounced in the ribbon blender.
- Paddles decrease sticking problems encountered in ribbon blenders and it also decreases the torque required for granulating and thus can handle wetter paste.
- Paddle blenders are often used as a continuous granulator and have both lower torque and more applications when compared to a continuous ribbon blender.
The two popular ribbon or paddle blender used as granulators are;
- The topogranulator: This is a batch-style ribbon blender with the ability to either compress or mechanically fluidize the granulation.
- The turbulizer: This is a continuous paddle granulator whose unit provides adjustable mixing, shear, and impact action based on the revolution per minute of the shaft and the angle of the impact blade.
ii. Planetary Mixer
Planetary mixers which are mainly used to mix medium viscous to high viscous media can also be used as granulating equipment. When used as a granulator, planetary motion of the mixer is generated by rotating the agitator off an assembly in a direction opposite to that of the rotation of the agitator assembly as it moves around the bowl. Despite the representations of planetary by different commercial names, like Hobart granulator, kitchen Aide granulator, etc, they still have the following basic makeup;
- Planetary motion
- Removable bowl
- Top-drive agitator
Planetary mixer tends to be better of mixing drying powders in a horizontal plane than in a vertical plane and so may require a distinct dry blending step prior to wet granulation.
iii. Orbiting Screw Granulator
Orbiting screw blender which is mainly used for dry mixing of powders when modified is used as a very gentle granulator mixer. The following modifications along with a chopper in the sidewall make orbiting screw blender an effective granulator for powders, slurries, suspensions, and pastes;
- The unit is fitted with a spray nozzle mounted on the agitator. This nozzle adds liquids to the dry powder.
- A sintered metal plate which allows entry of compressed air through the skin of the mixer or exhaust moisture to obtain drying.
iv. Sigma Blade Mixer
Sigma blade mixer is a compressive granulator designed for kneading, mixing, and homogenizing wet, pasty and high viscous materials. The two sigma shaped blades which sit horizontally and parallel at the bottom of the mixing trough rotates in opposite directions at different speeds.
This rotatory movement of the blades causes the material to be moved from blade to blade and from end to end generating /resulting in a figure-eight pattern of movement that produces a thorough powder mix. When used as a low shear granulator, the sigma blade mixer is proceeded by a dry mixer and the unit generates liquid added to the powder during granulation which facilitates the formation of uniform granules with binder matrix and good binder distribution.
References
- Dilip M. Parikh (2010). Handbook of Pharmaceutical Granulation Technology, Third Edition. CRC Press, Taylor and Francis Group, LLC.
- Jim Litster, and Bryan Ennis (2004). The Science and Engineering of Granulation Processes. Kluwer Academic Publishers, Dordrecht, Netherland.
- Larry, L. A. and Stephen, W. H. (2008), Pharmaceutical Dosage Form: Tablet. CRC Press, Taylor and Francis Group, LLC.
Getecha RS 6000 Series Large Part, High Throughput, Heavy Duty Granulators
The RS 6000 Series granulators are ideally suited to the following applications:

The RS 6000 Series Granulators are designed for applications requiring the best built, heavy-duty granulators for particularly demanding applications.
Up to 6,500+ pounds per hour throughput
24' diameter, segmented rotors
Widths up to 60 inches
Main Features:
Individual machine adjustment by modular design
Optimal accessibility for cleaning and servicing
Electro-hydraulic swinging up of the screen-carriage until the running roller touches the ground |
Screen cradle rolls on casters and with very little effort can be rolled completely out from the cutting chamber. With the screen cradle removed, access to the cutting chamber is unmatched.
Superior rotor design |
Note the reverse mounting style of the blades to the rotor shelf. By affixing the blades to the underside of the blade shelf, the blade positioned in reinforced during operation. With this mounting design, the lifting affect on blades in very heavy-duty applications is eliminated, greatly reducing the need to rebuild the rotor blade mounting shelves resulting in a significantly lower cost of ownership with the granulator.
Cutting-build design
Controls and electronics |
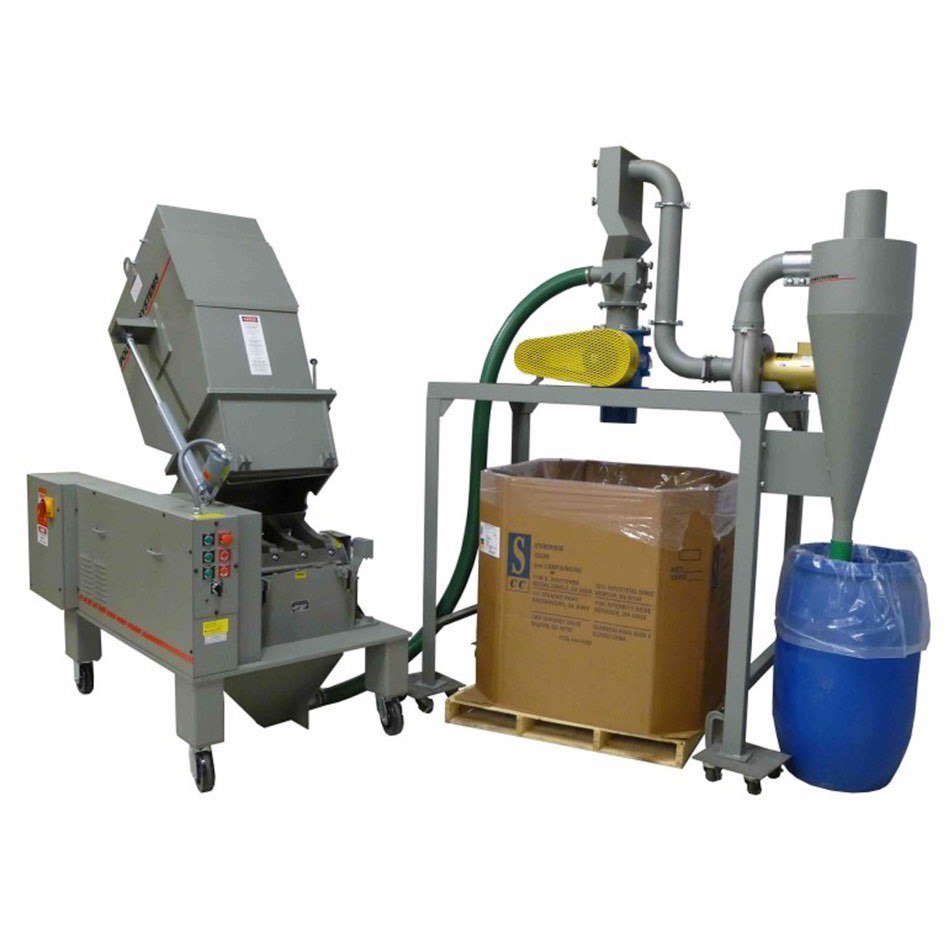
Machine Drawings (pdf files):
RS 6009_a1 standard unit with sound enclosureSAMPLE INSTALLATIONS:
Granulator Ii Ableton
INJECTION MOLDING:
TASK:
Granulating of automobile parts (bumpers, instrument panels and miscellaneous small parts)
Description of system:
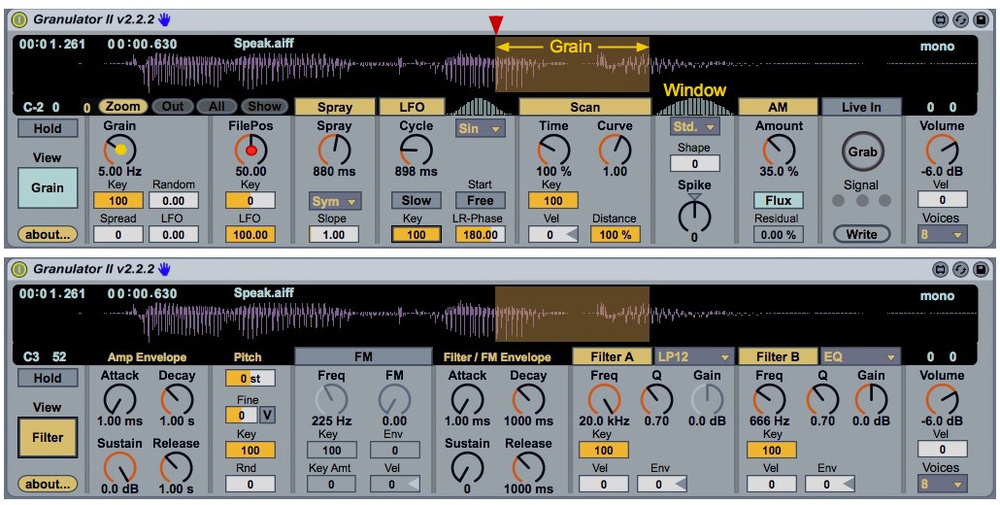
INJECTION MOLDING:
TASK:
Granulation of automotive parts in single man operated granulating room with limited space. Safety factor of operator falling onto conveyor belts and into granulator expressed by customer as major issue.
GETECHA SOLUTION:
The RS 6009 with a 85 HP motor was used for this application. For reasons of space, only a short conveyor belt and a hopper with lower inlet-height could be applied for the granulator II. The longest parts will therefore be granulated on granulator I.
Granulator Ii Download
Granulator I: Throughput 1400 lb/h, size of granulate 5 ± 1mm Parts with dimensions of up to 72' x 32', diagonal 80' Part weight up to 12 pounds
Granulator II: Throughput 1200 lb/h, size of re-granulate 5 ± 1mm Parts with dimensions of up to 58' x 7', diagonal 60' Part weight up to 5 pounds
Technical data: Conveying belts |

Granulators: - RS 6009 with 85 HP motor - Blades in HSS-quality, 64 HRC - Operation of the granulator through mobile hand-operating unit - Load-dependant control of the conveyor belts - Housing for the sound insulation of the granulators adapted to the granulator space. - Pneumatic conveyor for the conveyance of the granulator to the air-separation system |

Air separation systems: - The air separation blowers are fitted with frequency converters so that the optimal de-dusting level can be set in a very sensitive manner. - The exhaust air is filtered through the dust-sacks - The complete facility is grounded for the purpose of minimising static charge - The share of dust is stored in a closed plastic barrel. The barrel can be comfortably emptied. |
Getecha supplied the complete system, installed it at customer's site and performed initial operation together with the customer. In the process, the operating personnel were intensively trained. |
SAFETY ISSUE: To address the concern about the single operator safety factor, Getecha recommended a metal detecting pad at the entrance to the room. The procedure required any person entering the room be stand on the metal detector (located at the foot of the door) to insure the metal-toed shoes are being worn. When a person stands on the device with the metal-toed shoes, the door unlocks and allows for passage into the room. Due to the metal detectors on the conveyor belts, should an operator fall onto the conveyor belt, the belt will stop prior to the operator being transported to the granulator.
INJECTION MOLDING: LARGE BULKY PARTS
TASK:
GETECHA SOLUTION:
Conveyor belts- Angular-conveyor belts with ascendant part and 1m long horizontal part before the hopper inlet
- Single-fold metal-detector coil
Granulator: - RS 6012 with 90 hp motor - Blades in HSS-quality, 64 HRC - Operation of the granulator through mobile hand-operated unit - Load-dependant control of the conveyor belt - Press-in device: while feeding-in stacked-up chairs, they may fall apart in the hopper and block passage. Then, the operator activates a switch which runs the pneumatic press-in device in the hopper downwards. It presses the chairs into the open 3-blade-rotor. - Transport blower for discharge to the air separating system. |
Air separating system
- After the air separating system, the granulate falls through an all-metal separator into a small material container
- A second smaller suction unit then conveys it to a discharge height suitable for an octabin
Granulator 2
Prevention of part bridging in hopper: |
Granular Synthesis Ableton
EXTRUSION: HEAVY WALLED PIPING AND PIPE FITTINGS
TASK: - Granulation of pipes, tubes, start-up bars, fittings, - Dimensions: Fittings (photo right) |
GETECHA SOLUTION: - Granulator RS 6009 with 5 - blades - rotor |
Entrance to bypass hopper positioned on a permanent 12' X 20' platform outside the granulating room. One-way metal flyback curtains to prevent piping from being propelled back at operator
- load depending control for conveyor belt
- sound insulation
- Suction unit 2000 blower evacuation system
- Exhaust air dedusting GE 200 with metal separator
Shown with conveyor belt removed from feeding position. Note the blue barrels for the collection of dust from the air-dusting system for easy emptying of accumulated dust (see arrow)